|
ELECTRICAL DISCHARGE MACHINING (EDM) |
|
|
WHAT IS EDM? |
|
EDM (Electric Discharge Machining) is a NonConventional machining technique. Unlike conventional CNC machining which uses cutting knifes / tools, an EDM CNC machine shapes a workpiece by continuously charging electrons (electrical discharge / sparks) through electrodes. These sparks produce very high temperature that will erode the workpiece. Electrical control system ensures a fully controlled sparks that continuously erode and shape the workpiece. Dielectric liquid is used as a medium which functions to flush solid particles (the chips) from the erosion process, cooling the electrode and the workpiece, and as electricity conductor. |
|
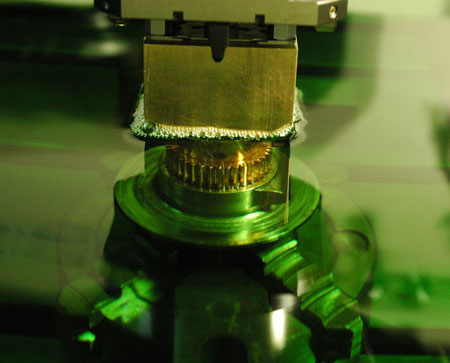 |
Sparks from the electrode |
|
|
HISTORY |
|
This technique was first discovered in 1770 by Joseph Priestly, a British scientist. However, his invention was still far from perfect and very inaccurate. Russian scientists then made further research in 1943 and found out that erosive process from sparks can be controlled and used for more accurate machining purposes. Development of modern EDM machines began during mid 1970’s, and started to be available for commercial use during mid 1980’s. |
|
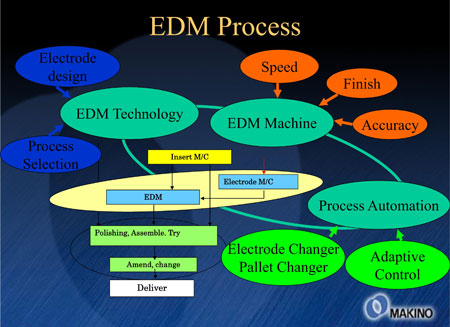 |
|
|
EDM MACHINE TYPES |
|
Wire EDM |
|
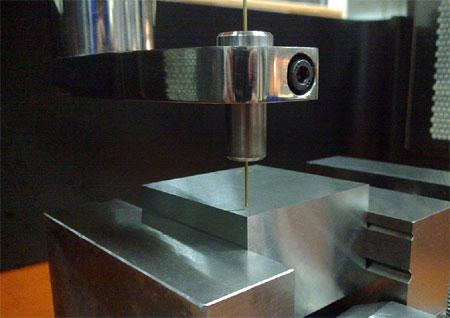 |
|
This EDM technique uses thin metal wire (usually made from brass). The wire electrode is connected to an electrical control system that produces controlled sparks that will erode the workpiece. Mechanical control system positions the wire electrode and the workpiece to make the desired cut. Wire EDM is usually used to make tools and die. |
|
Sinker EDM (A.K.A. Ram EDM) |
|
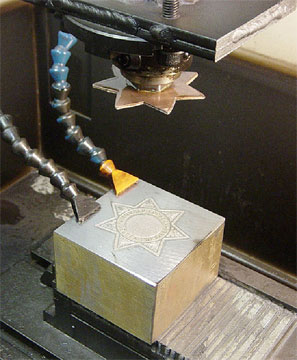 |
|
Using an electrode in the form of a negative die of the desired shape. The electrode is usually made from Copper or Carbon.
The electrode, which is connected to an electrical control system, is attached to a mechanical control system that moves and positions the distance between the electrode and the workpiece so that accurate sparks can occur. This EDM is used to make plastic moulds and deep & narrow cavities. |
|
|
ADVANTAGES OF EDM MACHINING |
|
 |
|
-
A cutting knife on conventional CNC Milling has a disadvantage that it cannot reach an area that is "deep and narrow". An EDM CNC can easily machine a workpiece with complex details & contours, very small holes, blind cavities, sharp corners, thin walls and cross sections, blind keyways, internal splines, squares and hexes, according to the shape of the electrode.
-
Modern Control System enables very accurate sparks that produce smooth surface (mirror finish) without the need for going through polishing and finishing processes.
-
Able to machine on workpieces with very hard or hardened materials, such as Aluminum, Brass, Carbide, Copper, Steel, Titanium, Hastalloy, Inconel and Stellite.
-
There is no physical contact between the electrode and the workpiece, so weak materials and complicated parts can be machined without distortion.
|
|
|
ADVANTAGES OF MAKINO HQSF |
|
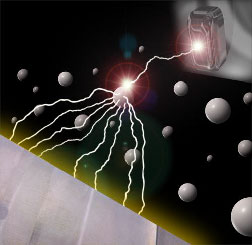 |
|
High Quality Surface Finish (HQSF) Technology from Makino, using Special Powder mixed with the dielectric liquid, producing much smoother surface than regular EDM CNC. |
|
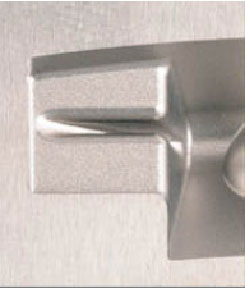 |
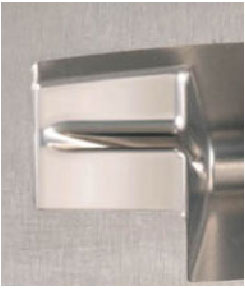 |
Without HQSF |
With HQSF – Very smooth surface |
|
|
|